not sure of the best or easiest way to cut the hole in a fairly heavy gauge powder coated enclosure without damaging the powder coat or having a crappy looking job done.
In the past, I'd put masking tape over the surface, marked it out using fine pen, then drilled a large hole somewhere inside the lines, and used a hand-held nibbling tool. Working up the the lines you can get a nice finish and dead square corners. Finish with a flat file, Peel the masking tape off and its done.
More recently, I've been using my lathe with a VMA and a small slot-drill to get an appropriate radius corner. If set up properly, the DRO lets you work to high precision (1/1000 of an inch if you wish, easily).
Here, I'm doing 4 panels at once.
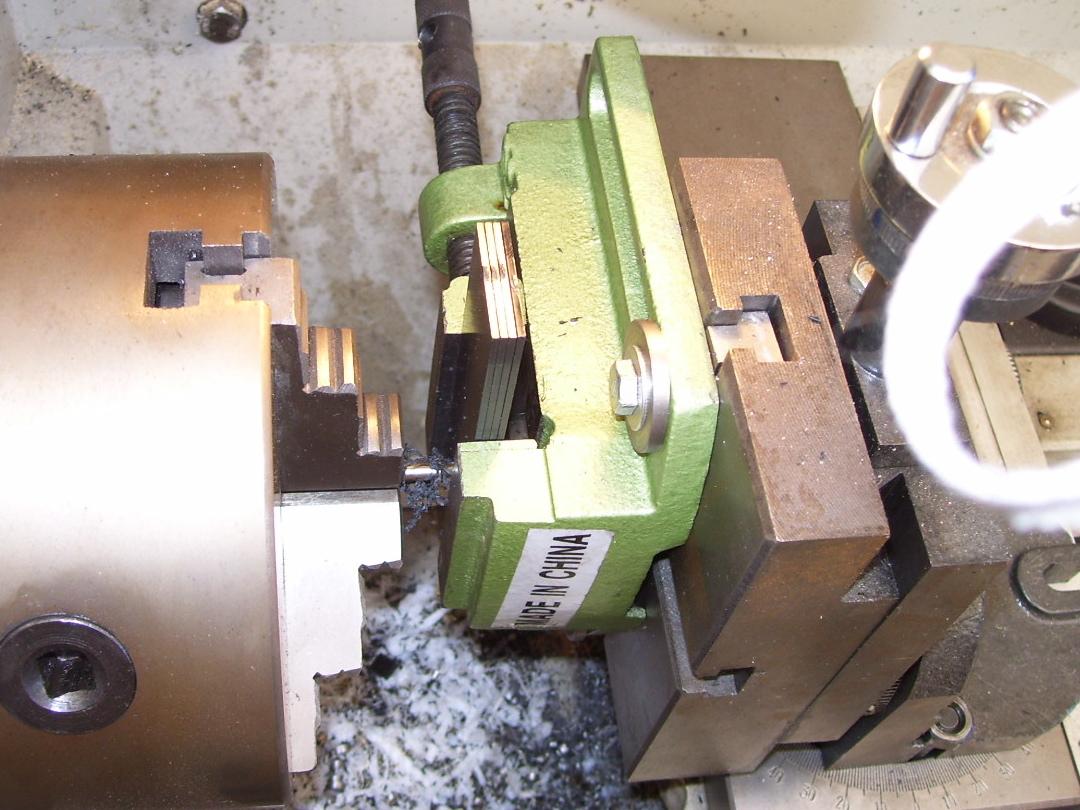
The cutout I required was smaller than yours, for the RJ45 connector. But they still turned out perfectly.
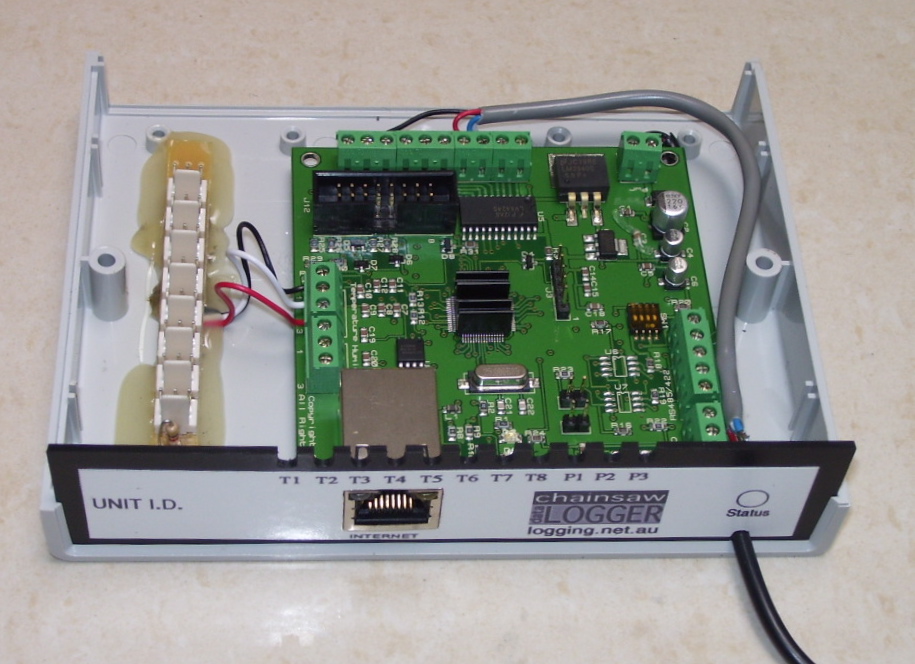